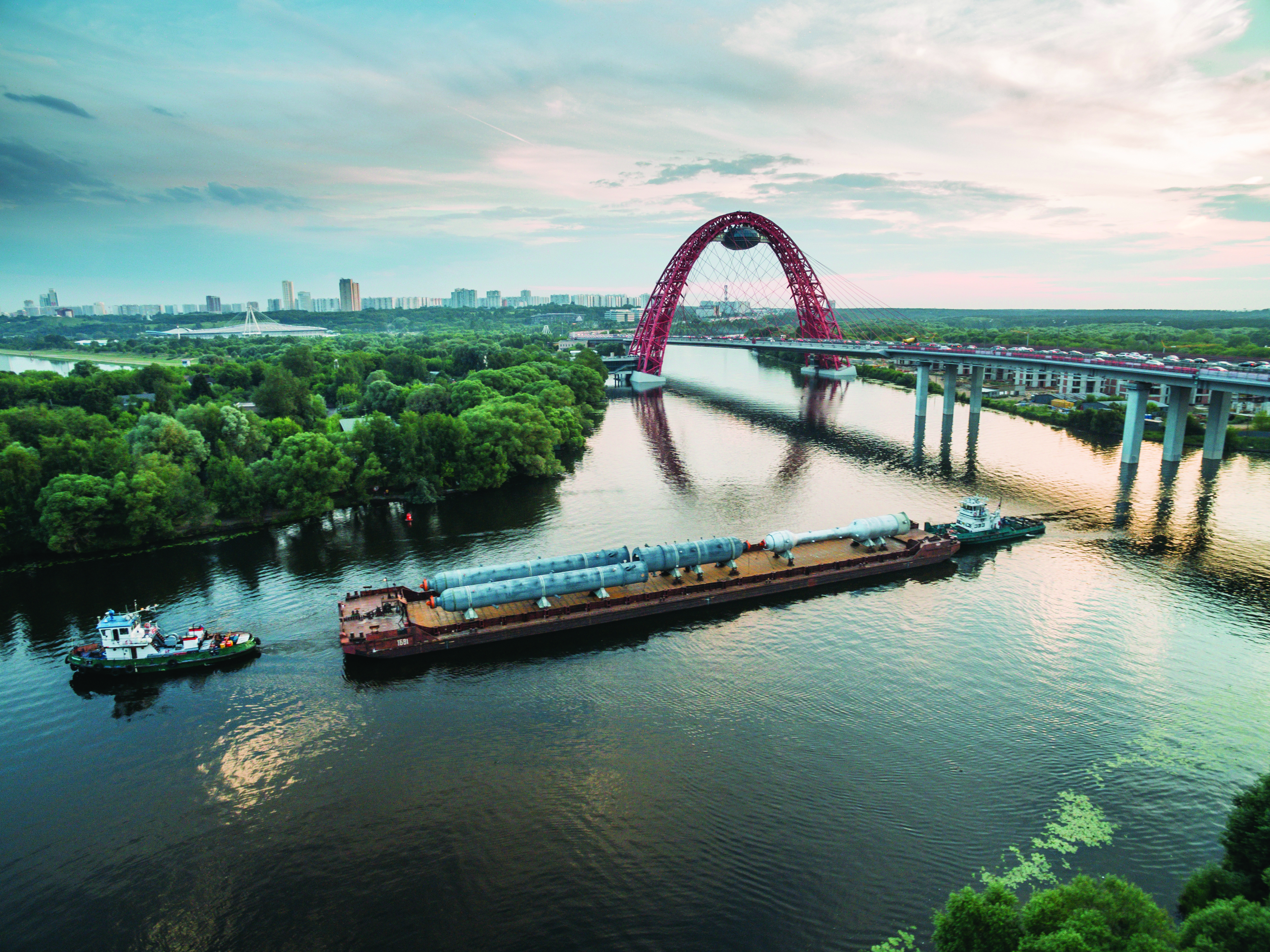
In February of 2018, Maire Tecnimont was awarded the design and construction of a 54 meter long column to be installed in Siberia. Here's how it went.
In mid-August, very important logistic operations for the Maire Tecnimont Group were successfully completed in Omsk, the seventh-largest city in Russia, located on the Irtysh river not far from the border with Kazakhstan. This was the final destination in the journey of a steel column that weighed over 100 tons and was 54 meters long.
The extraordinary and complex operation, started on July 10 in Brindisi and concluded forty days later in the heart of Siberia, took place entirely without resorting to roads or railways: a 15-story high and one hundred percent carbon steel column was delivered via seas and rivers for thousands of kilometers, transported on ocean merchant ships and river barges specifically designed for Siberian conditions.
Exceptional transportation
The oil treatment column is an element of the Omsk refinery, one of the most technologically advanced in the Russian Federation and among the largest in the world, with an overall crude oil treatment capacity of about 21.3 tons per year. Enrico Rolandelli, Tecnimont Engineering and Operation manager explains, “Since February 2018 we have had an EP+Cm contract for a new Delayed Coking Unit of the Refinery for our customer GazpromNeft: the unit will increase the conversion capacity of heavy residues, optimize the production of distillates and produce anode-grade coke in order to revamp the refinery for the production of Euro5 fuels. Thanks to this order, in addition to strengthening strategic collaboration with an important customer, we consolidate our presence in Russia as reliable suppliers of high value-added services for the local market”.
From Brindisi to Omsk in 40 days
The eight elements of the special transport supply were produced by qualified Italian companies with technical offices located in Cremona and Treviso, and production facilities in Brindisi and Vibo Valentia. Seven blocks, the smallest ones, measured between 20 and 38 meters long, while the column alone, consisting of two assembled pieces, exceeded 50 meters. A special electronically controlled trolley was used to transport it from the factory to the ship, taking one night to travel the three kilometers to the port of Vibo Marina at walking speed. The special freight then sailed to Brindisi, where the other components were loaded, and was finally bound for Russia.
“Recalling the various stages”, says Enrico Santi, “is useful for understanding the complexity of the situations to be managed and the high level of preparation of the entire project and operational chain. Departing from Puglia on 10 July, the freight traveled over four thousand kilometers: from the Mediterranean it passed through Gibraltar, circumnavigating Europe, Denmark and Norway and on into the North Sea. The column arrived at the Russian port of Sabetta (in the Yamal peninsula, at the Arctic Circle) twenty days later, and then on 3 August reached Novy Port, where it was transferred from ocean cargo freighter to the barges equipped to navigate the Russian rivers. A highly precise operation based on analyses aimed at optimizing the delicate loading and unloading phases of handling”.
Getting to Sabetta and Novy Port on time was just as strategic: the Ob and Irtysh rivers thaw window is only sixty days a year, from mid-July to mid-September. Making one wrong decision or even a single mistake could mean a twelve month delay on the project, with costs and penalties skyrocketing. The project director picks up: “Every engineer knows that analysis and planning are essential to reducing risks but cannot remove them altogether. In the brainstorming phase, imagining the greatest possible number of implications enabled us to manage each variable of the path. This time the unexpected event was fog, which forced the shipper to stop the barges for three nights, avoiding even worse damage and complication”.
On 20 August, after a little over two weeks, the freight finally arrived at Omsk customs docks, where it was held up for a few days due to the numerous, though expected, bureaucratic formalities. “Before being able to unload anything,” continues Santi, “it is necessary to verify that the materials match the mountain of papers attached to the supply. Work requiring great focus, especially in Russia, where flexibility and cold blood make the difference. In this case, an unexpected mistake was the size of an A4 sheet of paper, a document with a missing certification stamp. Fortunately, and this is no exaggeration, Italian engineers are second to none when it comes to a rush job. Thanks to a good amount of creative quick thinking, 72 hours later we had worked out a new procedure that helped us pass through customs”.
Arriving in Siberia
The last box of the transport list to check was the unloading and transfer of the columns with precision cranes from the barges to the motorized multi-wheeled carts. These vehicles delivered the load to its foundation, traveling four kilometers on the construction site roads. “The last fundamental micro-decisions were those taken to facilitate the transport of the pieces from the dock to the GazpromNeft plant. Bringing a 54-meter long steel element without encountering any unforeseen obstacles requires a careful study to calculate the minimum slopes, the radius of all curves, the width, and the bridges’ holding capacity. We reinforced and widened passages, paved dirt roads, removed traffic lights and raised electric cables. After this long journey, taking the wrong decision in the final stretch would have been a cruel joke. The ultimate success of the operation is to see the customer who, in a matter of minutes, agrees that everything took place in the time and manner agreed upon, with respect for all the quality and safety standards. Only we know, after twelve long months of hard work spanning from the design stage to the delivery, what is behind this project. And when the work ends, satisfaction runs from Siberia to Milan at the speed of light!”.
The mission was fully completed at the end of September, thanks to the expertise of the team that safely erected the column on its foundation. GazpromNeft and Maire Tecnimont have added another piece to their story of mutual collaboration. From the thirty degree weather of Puglia and Calabria to autumn in the heart of Russia: a steel column which fears no thermal change now stands at the Omsk plant. To the curiosity of Trans-Siberian travelers.
Choosing the path
The studies carried out over the years and the advanced skills in the field of logistics, including the recent Omsk project, have enabled us to take strategic decisions of great importance, opting for a naval transportation plan capable of managing oversize elements (difficult for land or rail delivery). “There were the issues of who needed to be involved along the way,” continues Rolandelli, “of what specialized documentation to prepare, of what scenarios and risk projections to draw. Among other things, when the job started a couple of years ago, the customer GazpromNeft had expressed the intention of sending the materials to Omsk using different routes from the usual ones. Their idea was to travel the Arctic route, which connects Norway to China, thanks to the new use of nuclear-powered icebreakers, with 350-megawatt engines capable of breaking three-meter-thick ice slabs”.
By choosing the northern sea route (the so-called ‘Polar Silk Road’ which enables a ship to navigate from Shanghai to Rotterdam in 33 days, rather than the 50 day journey through the Suez Canal), the project would have had totally different characteristics. “GazpromNeft’s initial goal was to involve Chinese suppliers and use this new route, but a delay in the inauguration of the Polar Silk Route created a stalemate. From our perspective, knowing the logistical issues within Russia, we preferred to repropose the routes and platforms already tested in other plants in Omsk, the latest of which was started only five years before. At the signing of the contract we made a series of decisions, convinced that our choices were functional to the best quality and parameters of the project: using our cost, risk and time assessments, we advocated for the excellence of our European supply chain, consisting of mostly Italian suppliers, to guarantee high and stable performance over time, even at polar temperatures as seen in Omsk. In fact, the accountability and leadership proffered, together with the framework of costs suited to the objectives, brought the expected results: the steel column arrived at the Jamal peninsula on time, right between the spring thaw and the river high. Then, it went straight on to the Omsk refinery”.
The phases of the project: from conception, construction, to installation
The operation was far from trivial, given the route, the potential risks and the transport case studies that had to be respected. Furthermore, the heavy authorization process may be added to the list of difficulties encountered. “We were ready with great commitment, adequate time and specific professional figures,” explains Enrico Santi, Tecnimont project director for the Omsk contract. “Everything starts from two phases: the more creative concept study and the ‘Project Execution Plan’. In our business - and this applies to every job - both the operational activities and the chances of reaching the goal depend on the quality of these two initial steps. The more imagination, experience, and creativity you invest in knowing exactly where you need to go, and how you need to get there, the fewer problems you’ll have along the way.
The first step we renamed “the think tank”, the typical brainstorming phase, where we analyzed all the variables and critical elements that may be encountered; the second is putting all the best ideas on paper according to the execution sequence. Following that prospectus, it is important to reiterate, every decision counts. The project leader, knowing the contract and the objective, gathers the logistic, procurement, transport, and construction representatives to exchange as many ideas and opinions as possible on the various activities. The comparison of experiences and individual differences helps to break down the implications step by step, thus starting to define a leaner and cleaner framework”.
After these two phases, the project control manager defines the sequences and the timing of the future stages. From now on - after the concept study and the executive plan - we move on to the third phase, that of the project engineering led by the project engineering manager. Half engineer and half manager with vast skills on both fronts, this professional has a great leadership capacity to perform the coordination, supervision and overall control of the works.
Santi continues: “In addition to defining the process mechanics, the operational phases, the tests and the inspections, the task force needs the contribution of the project procurement manager, who must select the suppliers, conduct the commercial negotiations and plan the purchases from an operational point of view. As one would imagine, every decision, even the slightest one, has a profound effect on the project: making mistakes or not updating the qualifications of a supplier (or incorrectly assessing the financial stability, production capacity or quality certifications) can mean a serious delay and a consequent increase in costs. This coordination work starts from the basic principle of the safety of all the people involved in the detailed operations: indeed, the safety plan was jointly prepared by the entire team involved in this project. For us, therefore, managing complex situations in conditions of uncertainty is a day-to-day business”.
The post-order activity, as part of the procurement, breaks down into quality inspections (to verify the conformity of the products purchased) and expediting (to monitor the progress and compliance with delivery schedules). After this phase, the product is ready for shipment and is handed over to the logistics department responsible for its delivery from the factory (in this case, Italy) to its foundation, inside the refinery in Omsk where the oil treatment column will be installed. Santi continues: “The four phases described are the result of a process that must be carried out with the utmost respect for timing, methods, quality, and safety. To achieve this, engineering and procurement - coordinated from the Milan and Moscow offices - worked impeccably, halving the average allotted time”.
A well-deserved reputation
This exceptional shipment encompassing original design solutions based on specific environmental characteristics is a symbolic case that helps us talk about the importance of each individual decision, the organizational support network and the accountability of each team member: from the project engineers, the safety manager up to the technician who controls the vehicle handling the column on the construction site.
“The excellent reputation of Maire Tecnimont in Russia does not come by surprise,” explains Rolandelli “but is a result of historical roots that started long ago, with dozens of plants built in the petrochemical, gas treatment and fertilizer sectors. In the 1970s, Russia wanted to make the most important cities in the Soviet Union self-sufficient, providing them with refineries, chemical plants and nuclear power plants. During the Perestroika period between the late 1980s and the early 1990s, I remember that in Moscow, Tecnimont was building a turnkey plant to convert propylene into polypropylene. Although it was an extremely precarious time regarding the matter of personal safety, we all stayed where we were and completed the project. At that time the shipment of materials was very complex, but we managed to arrange river deliveries of 80-meter long elements on the Moscow river passing right in front of the Kremlin. This episode, along with dozens of other examples, constitute our credentials for continuing to operate in Russia at the highest levels”.